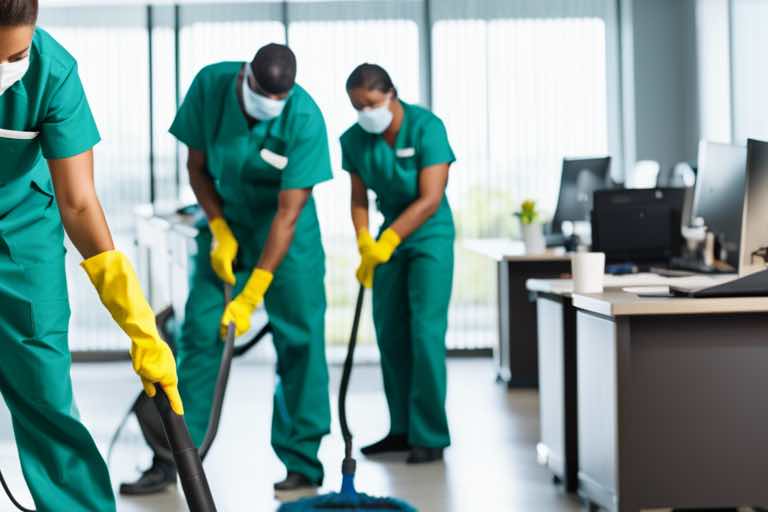
The Ultimate Guide to Facility Management: Industrial Best Practices
Do you find yourself juggling multiple tasks to keep your industrial facility running smoothly? From maintaining equipment to optimizing processes, the world of facility management is complex yet crucial for operational efficiency. Imagine a scenario where your maintenance costs are skyrocketing, and efficiency seems like a distant dream. This is where the importance of industrial best practices in facility management shines through.
Here’s a sneak peek at what you can expect from “The Ultimate Guide to Facility Management: Industrial Best Practices”:
🏭 Streamline Operations: Discover proven strategies and expert tips to enhance facility management efficiency in industrial settings.
🔧 Embrace Technology: Learn how to leverage IoT and data trends to reduce maintenance costs and extend the lifespan of your assets.
📊 Optimize Performance: Uncover examples of successful practices that can transform your facility management approach for the better.
Get ready to revolutionize your facility management processes and unlock a world of possibilities for improving performance and reducing costs.
Introduction to Facility Management Best Practices
Facility management plays a crucial role in ensuring the smooth operation and maintenance of industrial facilities. In today’s competitive landscape, implementing best practices is essential for optimizing efficiency, reducing costs, and maximizing the lifespan of assets. By following industry-leading methodologies, facility managers can enhance productivity, minimize downtime, and improve overall performance.
Implementing facility management best practices brings numerous benefits to industrial settings. Firstly, it enables proactive maintenance, ensuring that assets are regularly inspected and maintained, reducing the likelihood of unexpected breakdowns and costly repairs. Additionally, it improves space utilization, allowing for efficient layout design, proper equipment storage, and the creation of flexible workspaces. Effective facility management also involves maintaining an accurate asset inventory, ensuring that assets are tracked, assessed, and properly maintained according to predetermined schedules.
By digitizing and automating facility management operations, organizations can streamline processes and enhance productivity. This includes features like real-time asset tracking, streamlined work order management, and automated preventive maintenance scheduling. Leveraging IoT technology and predictive analytics facilitates predictive maintenance, optimizes energy efficiency, and empowers facility managers to make data-driven decisions. Furthermore, enabling mobile access to facility management systems allows for convenient on-the-go access to critical information, improving overall operational efficiency.
Overall, facility management best practices not only optimize facility efficiency but also result in cost savings, improved asset management, and enhanced coordination between teams. By embracing these practices, industrial facilities can establish a solid foundation for success and maintain a competitive edge in today’s fast-paced business environment.
Communicate With Internal Teams and Vendors
Effective communication is crucial for successful facility management operations in industrial settings. It enables smooth collaborations and ensures that all teams and stakeholders are aligned towards common goals. Here are some key tips to improve communication within your facility management:
1. Establish Clear Channels of Communication
Create a structured communication system that allows for efficient information exchange. Designate specific channels for different types of communication, such as email for formal correspondence, instant messaging for quick updates, and meetings for in-depth discussions.
2. Foster Open and Transparent Dialogue
Encourage open communication within your facility management teams. Emphasize the importance of voicing concerns, asking questions, and sharing ideas. Foster an environment where everyone feels comfortable expressing their thoughts and opinions.
3. Define Roles and Responsibilities
Clearly define roles and responsibilities within your facility management teams to avoid confusion and enhance accountability. Ensure that each team member understands their specific tasks and knows who to reach out to for support or information.
4. Share Regular Updates and Reports
Provide regular updates and reports to both internal teams and vendors to keep them informed about the status of facility management operations. This helps in maintaining transparency and ensures that everyone is on the same page regarding progress, challenges, and upcoming projects.
5. Conduct Effective Meetings
Hold structured and productive meetings to discuss important matters related to facility management. Share agendas in advance, encourage active participation, and allocate time for questions, concerns, and brainstorming. Follow up with clear action items and deadlines.
Remember, effective communication is key to fostering collaboration, minimizing misunderstandings, and driving operational efficiency within your facility management teams. By implementing these communication strategies, you can ensure smooth operations and successful collaborations with both internal teams and vendors.
Set and Manage Team Structure
Establishing an efficient team structure within facility management is crucial for smooth operations and successful outcomes. Here are some insights on how to achieve this:
Define Clear Roles and Responsibilities
Clearly define the roles and responsibilities of each team member involved in facility management. This ensures that everyone understands their tasks and contributes effectively to the overall goals. Assign specific duties related to maintenance, inspections, planning, and coordination.
Foster Collaboration and Teamwork
Encourage collaboration and teamwork among team members. Facilitate effective communication channels, both formal and informal, to promote knowledge sharing and problem-solving. Regularly conduct team meetings and encourage open dialogue to address challenges, brainstorm solutions, and celebrate successes together.
Establish a Reporting Structure
Determine a reporting structure that outlines how information flows within the team. This helps to maintain transparency, accountability, and clear channels for feedback and decision-making. Clearly define reporting relationships and ensure that each team member knows who they report to and who their direct reports are.
Foster a Positive Team Culture
Build a positive team culture that promotes trust, respect, and a sense of belonging among team members. Encourage open communication, actively listen to team members’ input and suggestions, and provide opportunities for professional growth and development. Recognize and reward individual and team achievements to boost morale.
By setting and managing a well-defined team structure, facility management teams can work together seamlessly, leverage individual strengths, and enhance overall performance to achieve their objectives.
Manage Risks and Returns
Managing risks and ensuring returns are essential aspects of successful facility management in industrial settings. By implementing effective strategies, facility managers can minimize potential hazards and maximize the value generated from their assets. Here are some key practices to consider:
Conduct Regular Inspections
Regular inspections help identify potential risks and maintenance needs. By conducting routine checks on equipment, systems, and infrastructure, facility managers can proactively address any issues before they escalate. This includes inspecting electrical systems, plumbing, HVAC units, and structural integrity.
Implement Emergency Preparedness Measures
Having a comprehensive emergency preparedness plan in place is crucial for industrial facilities. This plan should include protocols for handling emergencies such as fires, natural disasters, or security breaches. Conducting drills and training exercises can ensure that employees are well-prepared to respond swiftly and effectively during critical situations.
Maintain Documentation and Record-Keeping
Accurate documentation plays a vital role in managing risks and returns. Facility managers should maintain records of inspections, maintenance activities, and repairs. This documentation provides a historical perspective and aids in tracking trends, identifying recurring issues, and making informed decisions.
Collaborate with Contractors and Vendors
Building strong relationships with contractors and vendors is essential for managing risks and achieving positive returns. Working closely with trusted partners ensures that maintenance, repair, and upgrade activities are carried out efficiently and in accordance with industry standards. Regular communication and clear expectations contribute to a smooth and successful collaboration.
Remember, managing risks and returns in facility management requires a proactive approach. By conducting regular inspections, implementing emergency preparedness measures, maintaining accurate documentation, and collaborating with contractors and vendors, facility managers can mitigate risks and optimize returns in industrial settings.
Improve Space Utilization in the Workplace
Efficient space utilization is crucial in industrial settings to maximize productivity and optimize operations. Here are some tips to help you make the most of your workspace:
Efficient Layout Design
– Analyze your workflow: Understand the sequence of tasks in your operations and design the layout accordingly.
– Minimize movement: Organize workstations and equipment in a way that reduces unnecessary movement and promotes efficiency.
– Consider safety regulations: Ensure that your layout adheres to safety guidelines and provides clear pathways for employees and materials.
Proper Equipment Storage
– Utilize vertical space: Install shelving units or racks to maximize vertical storage and keep equipment off the floor.
– Categorize items: Use clear labels and designated storage areas for different types of equipment to improve accessibility and organization.
– Implement a maintenance system: Regularly inspect and maintain storage areas to prevent clutter and ensure equipment is in good condition.
Flexible Workspaces
– Embrace modular furniture: Use versatile furniture that can be easily rearranged to accommodate changing needs and workflows.
– Foster collaboration: Create open areas where employees can gather for discussions or brainstorming sessions.
– Incorporate break areas: Provide designated spaces for employees to relax, recharge, and socialize, which can contribute to productivity and overall well-being.
By implementing these space utilization strategies, industrial facilities can optimize their operations, improve efficiency, and create a more organized and functional workspace.
Establish Asset Inventory
Maintaining an accurate asset inventory is crucial for effective facility management in industrial settings. By diligently tracking assets and conducting regular assessments, you gain a comprehensive understanding of your facility’s resources and their condition. This enables you to make informed maintenance decisions and allocate resources efficiently.
Key steps to establishing an asset inventory include:
1. Tracking Assets
Document all equipment, machinery, and systems within your facility. Assign unique identification numbers or codes to each asset for easy identification and tracking.
2. Conducting Regular Assessments
Regularly evaluate the condition and performance of assets to identify potential issues and plan maintenance activities. This includes conducting inspections, collecting data on asset performance, and prioritizing maintenance tasks.
3. Implementing Maintenance Plans
Create tailored maintenance plans for each asset based on its unique requirements and criticality. Incorporate preventive and predictive maintenance strategies to minimize unexpected failures and extend asset lifespan.
Maintaining an accurate asset inventory empowers facility managers to identify maintenance needs, optimize resource allocation, and plan for long-term asset management. Successful facility management starts with a solid understanding of the assets under your care, allowing you to ensure smooth operations and maximize efficiency.
Digitize and Automate Your FM Operations
In today’s fast-paced industrial landscape, facility management (FM) professionals are increasingly turning to digitization and automation to optimize their operations. By leveraging technology, including advanced software and IoT devices, organizations can streamline their FM processes, enhance efficiency, and achieve better results. Here are some key benefits of digitizing and automating your FM operations:
Asset Tracking and Management
One of the primary advantages of digitization is the ability to track assets accurately and manage them effectively. With the help of asset management software, FM teams can easily monitor the condition, location, and lifecycle of critical equipment and infrastructure. This allows for proactive maintenance, reduces downtime, and improves overall asset performance.
Work Order Management
By transitioning from manual work order processes to electronic systems, facility managers can eliminate paperwork and streamline work order management. Digitizing work orders enables easy assignment, tracking, and completion of tasks. It also provides real-time visibility into the status of work requests, simplifying communication between FM teams, technicians, and stakeholders.
Preventive Maintenance Scheduling
Automating preventive maintenance scheduling ensures that equipment is regularly serviced and inspected, reducing the likelihood of unexpected failures. Utilizing software solutions, FM professionals can create maintenance plans, assign tasks, and receive automated reminders for upcoming inspections or replacements. This proactive approach extends the lifespan of assets, minimizes downtime, and lowers maintenance costs.
Data-Driven Decision Making
Digitization generates a wealth of data that can be analyzed to drive informed decision-making. By employing analytics tools, facility managers can gain valuable insights into maintenance trends, energy efficiency, and resource allocation. This data-driven approach allows for better planning, optimizing resources, and identifying areas for improvement.
Embracing digitization and automation in FM operations revolutionizes the way industrial facilities are managed. It enables enhanced asset tracking, efficient work order management, proactive maintenance scheduling, and data-driven decision-making. By harnessing the power of technology, organizations can achieve improved efficiency, cost savings, and overall effectiveness in their facility management practices.
Implement a Preventive Maintenance Plan and Increase Your Assets’ Lifespan
In industrial facility management, implementing a preventive maintenance plan is crucial for ensuring the longevity and optimal performance of your assets. By proactively addressing maintenance needs and conducting regular inspections, you can minimize downtime, reduce repair costs, and maximize the lifespan of your equipment and facilities. Here are some key steps to help you effectively implement a preventive maintenance plan:
Conduct a comprehensive asset inventory and assessment
Before creating your preventive maintenance plan, it’s essential to have a thorough understanding of your assets. Conduct a comprehensive inventory of all equipment, machinery, and systems in your facility. Include relevant details such as model numbers, installation dates, and maintenance history. This detailed inventory will serve as a foundation for your preventive maintenance plan.
Identify critical assets and prioritize maintenance tasks
Not all assets require the same level of maintenance. Identify your critical assets – those that significantly impact operations or carry high replacement costs – and prioritize their maintenance tasks. Develop a schedule that ensures regular inspections, cleaning, lubrication, and calibration of these assets. Focus on addressing potential issues before they escalate into major breakdowns or failures.
Set maintenance intervals and tasks
Based on manufacturer recommendations, industry best practices, and historical data, establish maintenance intervals for specific assets. These intervals should reflect the optimal frequency for inspections, servicing, and parts replacement. Define the necessary tasks for each interval, such as filter replacement, belt tightening, or software updates.
Utilize a computerized maintenance management system (CMMS)
A CMMS can greatly enhance the effectiveness of your preventive maintenance plan. It enables you to schedule and track maintenance tasks, assign responsibilities, and generate work orders. With a CMMS, you can set automated reminders for upcoming maintenance activities, track completed tasks, and monitor the overall maintenance performance.
Regularly analyze maintenance KPIs and metrics
Track key performance indicators (KPIs) and metrics related to preventive maintenance to evaluate the effectiveness of your plan. Monitor metrics such as asset downtime, mean time between failures (MTBF), and overall equipment effectiveness (OEE). Analyzing these data points will help you identify areas for improvement and make data-driven decisions to optimize your maintenance processes.
By implementing a preventive maintenance plan and following these steps, you can significantly extend the lifespan of your assets, reduce unplanned downtime, and optimize maintenance costs. Remember, preventive maintenance is an ongoing process that requires continuous monitoring, evaluation, and adjustment. Stay proactive, stay organized, and reap the long-term benefits of a well-maintained industrial facility.
Leverage IoT Technology and Predictive Analytics
In today’s industrial landscape, leveraging IoT technology and predictive analytics has become increasingly vital for facility management. By harnessing the power of these innovative solutions, facility managers can optimize processes, enhance energy efficiency, and enable proactive maintenance strategies.
Enhancing Facility Management Processes
IoT technology enables the seamless integration and connectivity of various devices within a facility. Sensors, actuators, and other smart devices collect valuable data in real-time, providing insights into the performance and condition of critical assets. This wealth of information empowers facility managers to make data-driven decisions and optimize their operations.
Improving Energy Efficiency
One of the significant advantages of leveraging IoT technology in facility management is the ability to improve energy efficiency. Smart sensors and automated systems monitor energy consumption patterns and detect inefficiencies or anomalies. Facility managers can then implement energy-saving measures and adjust resource allocation accordingly, leading to substantial cost savings and a reduced carbon footprint.
Enabling Proactive Maintenance
Predictive analytics plays a crucial role in facility management by enabling proactive maintenance. By analyzing historical data and performance patterns, predictive models can identify potential equipment failures or maintenance needs before they occur. This proactive approach allows facility managers to schedule maintenance activities strategically, minimize downtime, and extend the lifespan of assets.
With the integration of IoT devices and predictive analytics, facility managers can take a proactive stance in their maintenance strategies, resulting in improved operational efficiency, reduced costs, and optimized asset lifespan.
> “IoT technology and predictive analytics have revolutionized facility management. By leveraging real-time data and predictive models, facility managers can optimize processes, improve energy efficiency, and proactively maintain critical assets.”
Enable Mobile Access
In the fast-paced world of facility management, having access to critical information on the go is crucial for maintaining smooth operations. Enabling mobile access to facility management systems and tools is essential in today’s digital age. Here’s why it matters:
Enhancing Productivity
By providing facility managers and team members with mobile access to relevant data and resources, tasks can be accomplished efficiently and promptly. Whether it’s accessing work orders, tracking maintenance activities, or managing asset inventory, the convenience of mobile access empowers facility management teams to stay productive while on the move.
Real-Time Updates
Mobile access ensures that facility managers have immediate access to real-time data, enabling them to make informed decisions quickly. Whether it’s addressing an urgent maintenance issue or responding to a visitor management request, the ability to receive updates and notifications on mobile devices ensures prompt action and smooth coordination.
On-the-Go Collaboration
Enabling mobile access facilitates seamless collaboration among facility management teams, vendors, and other stakeholders. Through mobile devices, team members can easily communicate, share updates, and collaborate on projects, regardless of their physical location. This enhances teamwork and enables efficient problem-solving even when team members are dispersed.
Data-Driven Insights
Mobile access to facility management systems allows for easy retrieval and analysis of important data and analytics. Facility managers can monitor key metrics, track performance indicators, and gain valuable insights into maintenance operations and resource allocation. These data-driven insights empower facility managers to make informed decisions, streamline processes, and drive continuous improvement.
Mobile access in facility management is more than just a convenience; it enhances productivity, enables real-time updates, fosters collaboration, and provides valuable data insights. Embracing mobile technology empowers facility management teams to effectively address challenges, respond promptly to changing circumstances, and optimize operations in industrial settings.
Make Use of Data and Analytics
Data and analytics play a crucial role in effective facility management decision-making. By leveraging data-driven insights, facility managers can optimize maintenance planning, resource allocation, and overall operational efficiency. Here’s why utilizing data and analytics is essential in facility management:
1. Evidence-based decision-making:
Data and analytics provide objective and reliable information that helps facility managers make informed decisions. By analyzing historical data, trends, and patterns, managers can identify areas for improvement, track key performance indicators (KPIs), and prioritize maintenance activities.
2. Resource optimization:
With access to real-time data, facility managers can allocate resources more effectively. By monitoring equipment performance, energy consumption, and occupancy patterns, they can identify opportunities to reduce waste, streamline operations, and lower costs.
3. Proactive maintenance:
Analyzing data allows facility managers to move from reactive to proactive maintenance strategies. By monitoring asset health and performance indicators, managers can detect early warning signs of malfunctions, plan preventive maintenance activities, and avoid costly breakdowns.
4. Performance tracking:
Data and analytics enable facility managers to track and measure the performance of various systems, processes, and service providers. This helps identify bottlenecks, assess the effectiveness of maintenance programs, and make data-driven decisions to improve overall facility performance.
By harnessing the power of data and analytics in facility management, organizations can optimize operations, reduce costs, and enhance the overall maintenance strategy. Ensuring accurate data collection, reliable analytics tools, and effective interpretation are key to unlocking the full potential of data-driven facility management.
[Related terms: facility management software, facility management tracker, facility management checklist, facility management solutions, facility management tools, facility management app, predictive analytics for facility management]Take a Customized FM Approach
In the realm of facility management (FM), adopting a customized approach is crucial for industrial settings. Each industrial facility comes with its unique set of needs, challenges, and goals, requiring tailored strategies to ensure optimal efficiency and performance. By considering the specific requirements of the industry, facility managers can design management practices that address the intricacies of their operations. It involves understanding the distinctive demands of industrial environments, such as compliance regulations, safety measures, and equipment maintenance. This tailored approach allows facility managers to develop proactive solutions that align with the industry’s best practices while considering the limitations and opportunities presented by the facility. By customizing facility management strategies, industrial settings can effectively streamline processes and maximize operational output.
– Consider Industry-Specific Challenges
– Analyze Compliance and Safety Requirements
– Identify Equipment and Maintenance Needs
– Develop Proactive Solutions
– Align with Best Practices for Industrial Environments
Remember, adopting a customized FM approach ensures that facility management practices cater specifically to the unique demands of industrial settings, resulting in enhanced performance and operational efficiency.
Conclusion
Implementing facility management best practices in industrial settings is crucial for optimizing operations, improving efficiency, and reducing costs. By following these expert tips, you can streamline your facility management processes and maximize the lifespan of your assets.
Key takeaways from this guide include:
1. Effective communication is vital for smooth operations and collaboration between facility management teams and internal/external stakeholders.
2. Establishing an efficient team structure, defining roles and responsibilities, and fostering teamwork contribute to successful facility management.
3. Regular inspections, emergency preparedness measures, and risk management strategies help mitigate potential risks and ensure returns in industrial facility management.
4. Optimizing space utilization through efficient layout design, proper equipment storage, and flexible workspaces enhance productivity and efficiency.
5. Maintaining an accurate asset inventory, tracking assets, and implementing maintenance plans contribute to improved asset management.
6. Digitizing and automating facility management operations, such as asset tracking, work order management, and preventive maintenance scheduling, offer numerous benefits.
7. Organizing preventive maintenance tasks, extending asset lifespan, and tracking maintenance KPIs help reduce downtime and improve operational efficiency.
8. Leveraging IoT technology and predictive analytics improves energy efficiency, enables proactive maintenance, and optimizes facility management processes.
9. Enabling mobile access to facility management systems and tools enhances productivity and provides on-the-go access to critical information.
10. Utilizing data and analytics for decision-making supports maintenance planning and resource allocation in facility management.
11. Customizing facility management strategies to fit the unique needs and challenges of industrial settings is essential for success.
By implementing these best practices, you can optimize facility management in industrial settings, reduce costs, improve efficiency, and ensure the smooth operation of your facilities.
How Best Practices in Facilities Management are Determined
Determining best practices in facilities management is a process that relies on industry expertise and successful case studies. By analyzing the experiences and outcomes of various facility management approaches, industry professionals can identify strategies and methodologies that consistently yield positive results. These best practices are then shared and adopted by facility managers seeking to optimize their operations and improve overall performance.
Industry experts contribute to determining best practices by studying successful facility management implementations and identifying common patterns and approaches that have proven effective. These insights are often consolidated into guidelines and frameworks that serve as benchmarks for facility managers, providing them with a solid foundation for decision-making and strategic planning.
Moreover, successful case studies play a crucial role in identifying and promoting best practices. Real-world examples showcase how specific facility management strategies were implemented and the positive impact they had on organizations. These case studies provide tangible evidence of the benefits derived from implementing certain practices, helping facility managers gain insights into what works and what doesn’t.
It’s important to note that best practices are not static. As the industry evolves and new technologies, methods, and trends emerge, the definition of best practices also evolves. Facility managers should stay informed about the latest developments in the field and adapt their practices accordingly to stay competitive and maximize efficiency.
By leveraging industry expertise and drawing insights from successful case studies, facility managers can determine and implement the best practices in facilities management that are most relevant to their specific needs and goals.
Are you ready to elevate your facility management practices to new heights? Don’t let this opportunity pass you by! Join VATES Facilities Support WLL Bahrain in leading the charge toward operational excellence and unparalleled service quality. Whether you’re seeking to refine your existing operations or to lay the groundwork for future success, our ultimate guide to facility management has the insights and strategies you need. Act now to transform your facility management approach with industry best practices that set the standard for excellence. Contact VATES Facilities Support WLL Bahrain today to learn how we can assist in optimizing your operations, enhancing safety standards, and ensuring the highest level of client satisfaction.
Don’t settle for average when you can achieve extraordinary results. Reach out to VATES Facilities Support WLL Bahrain and take the first step towards a more efficient, safer, and more successful facility management future. Your journey to the top begins with us. Embark on your journey to operational excellence with VATES Facilities Support WLL Bahrain – where your facility’s potential becomes a reality. Reach us today at info@vfsupport.com
Leave a Reply